How can our existing building stock become energy-efficient and resilient?
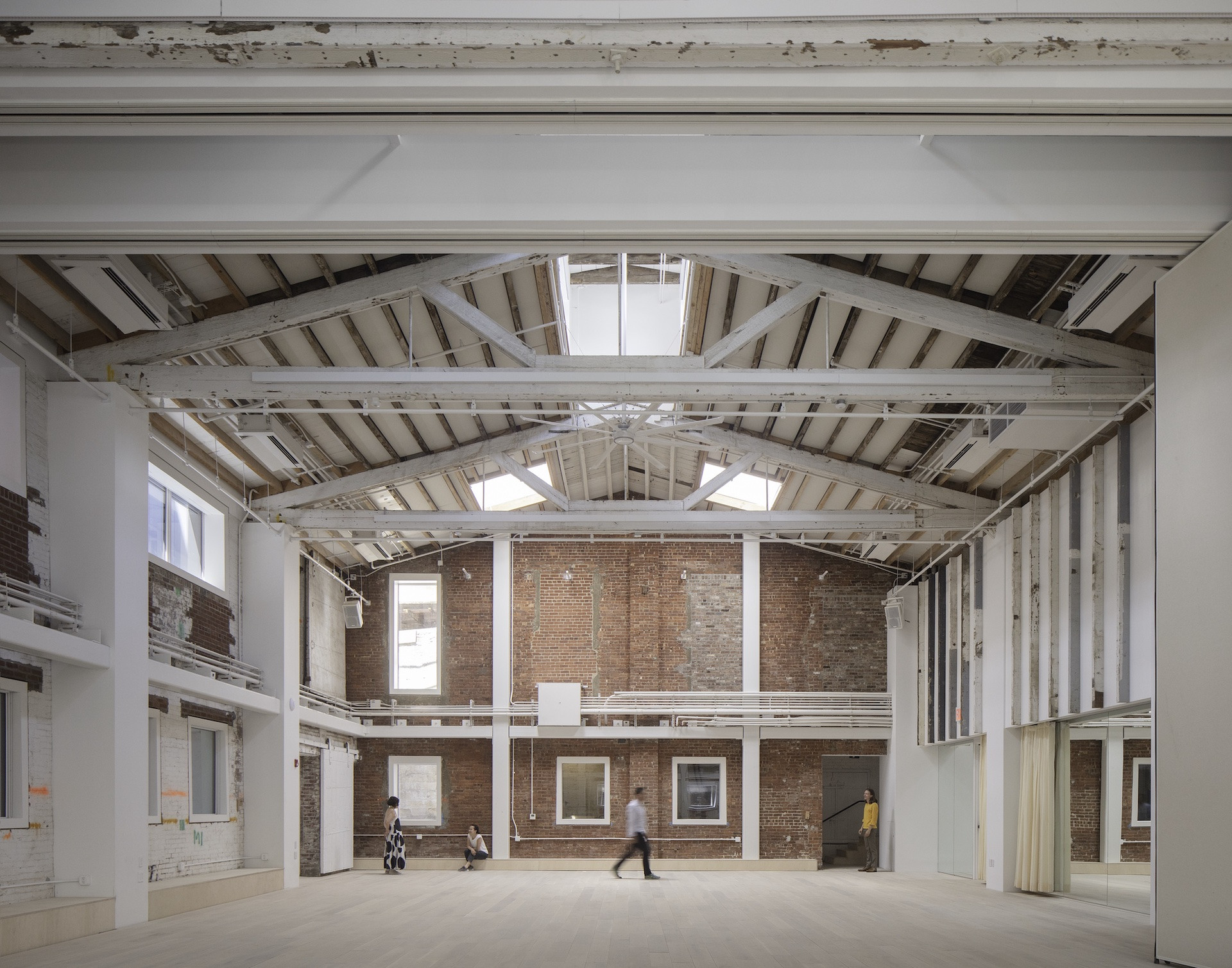
Specializing in retrofitting existing building stock to become more energy-efficient, self-sufficient, and resilient, NYC-based studio Co Adaptive develops strategies to minimize
Create a free account to read the full article
Get 2 premium articles for free each month
Related Articles
MORE Sustainability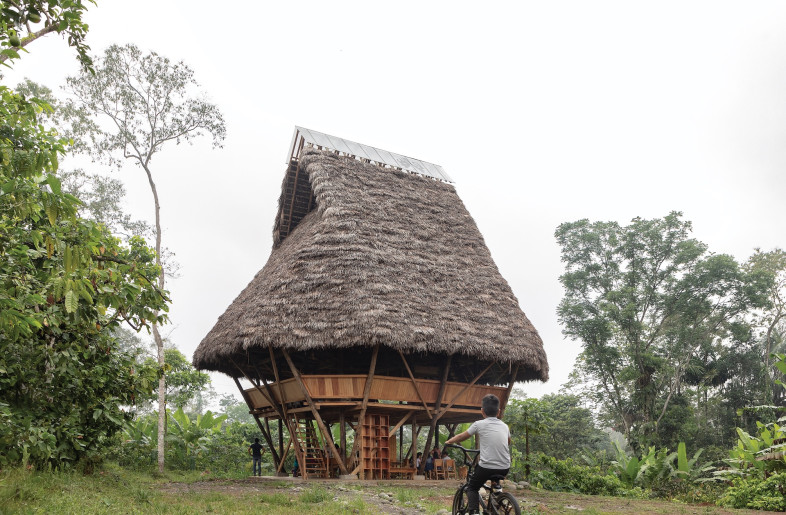
In the climate conversation, low-tech architecture is leading the way in South America
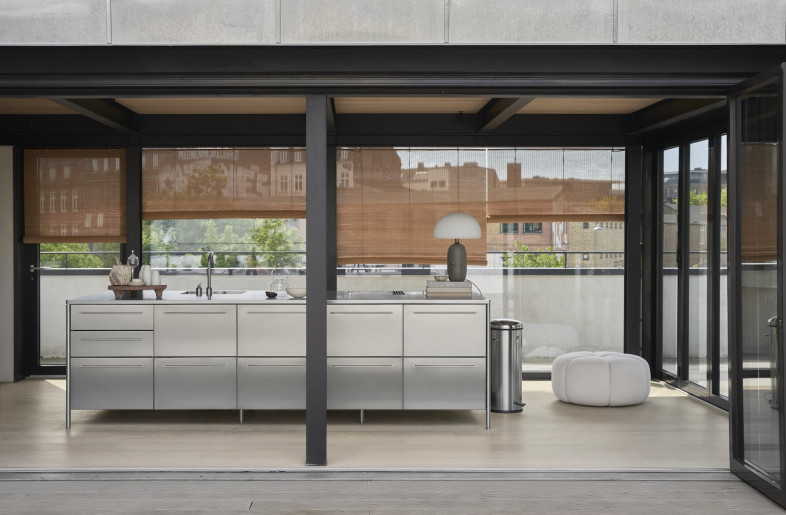
These 7 future-ready kitchens show that adaptable design and functionality are the new standard
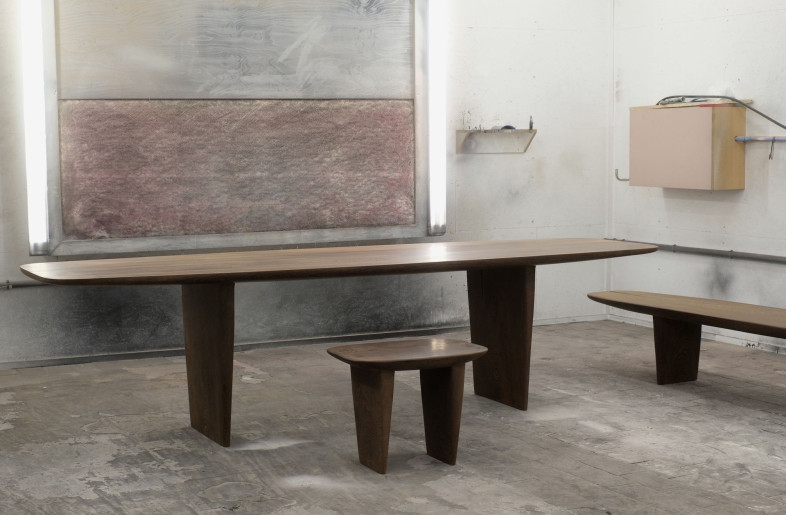
By narrowing the production radius, a Belgian studio minimizes environmental impact, maximizes terroir
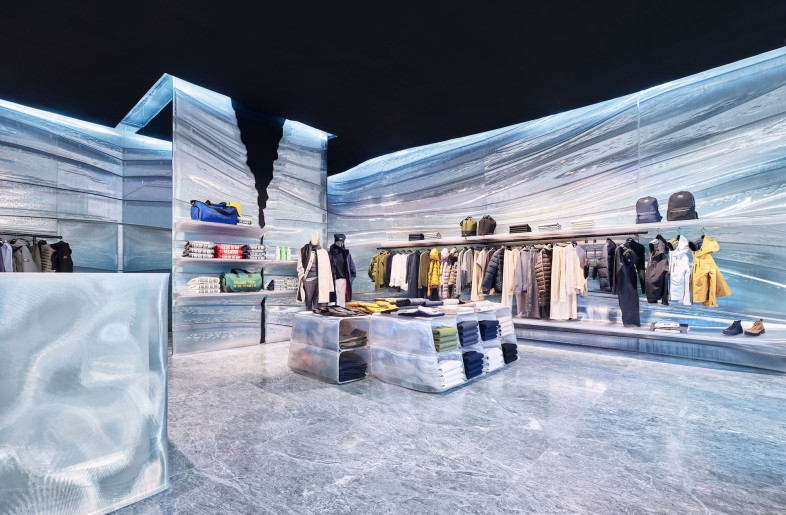
What retailers can do to cultivate conscious consumerism
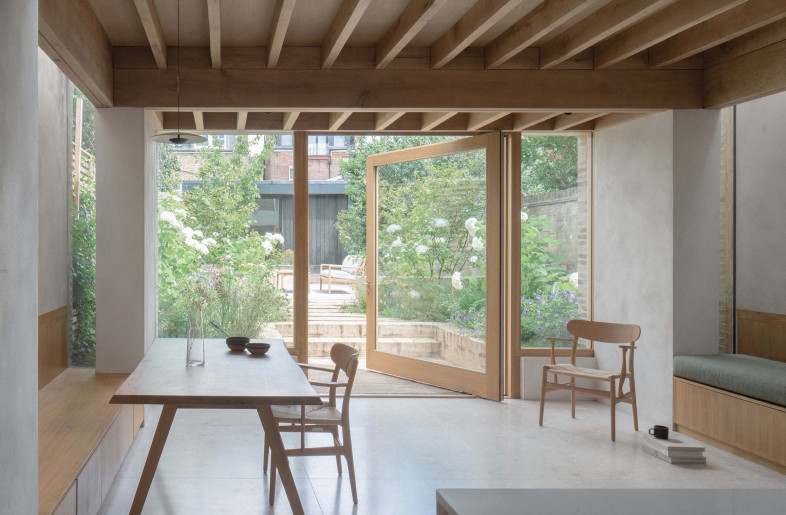
The renovation of a London Victorian home enables sustainable, seamless living
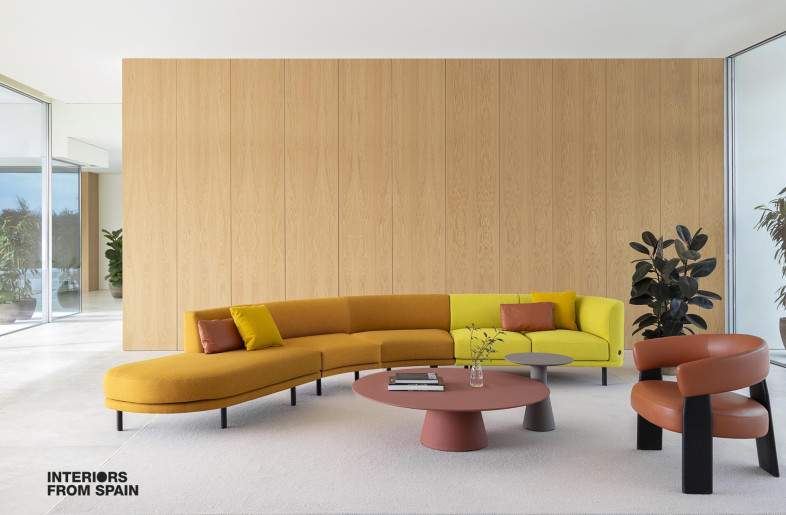
Andreu World’s 70-year legacy is a milestone in responsible furniture design
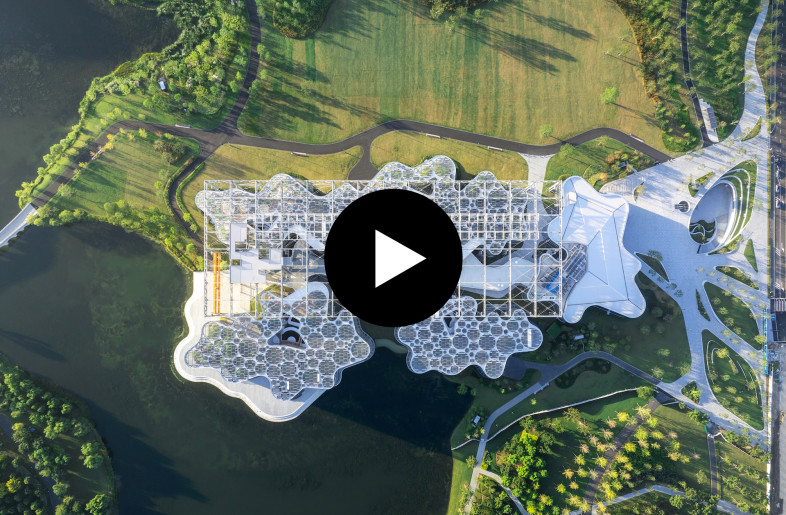
Video: Is urban biodiversity attainable? This steel-factory-turned-greenhouse shows how
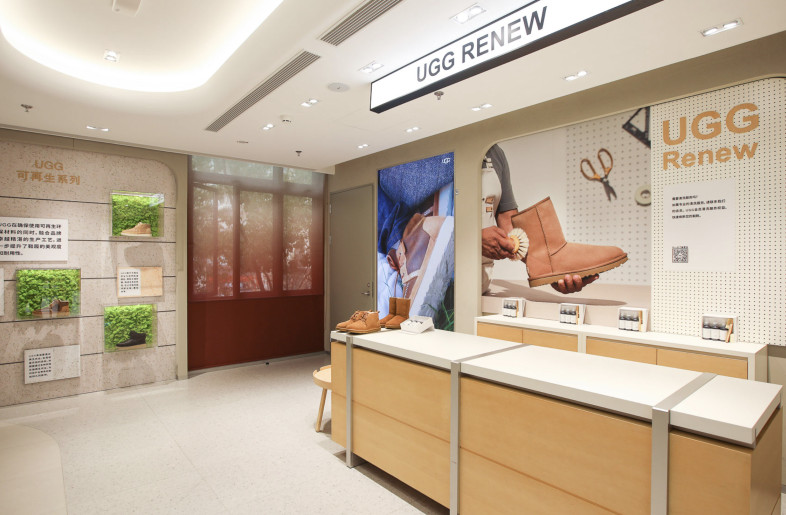
Report Recap: How modern living, work and play practices will manifest in our built environment
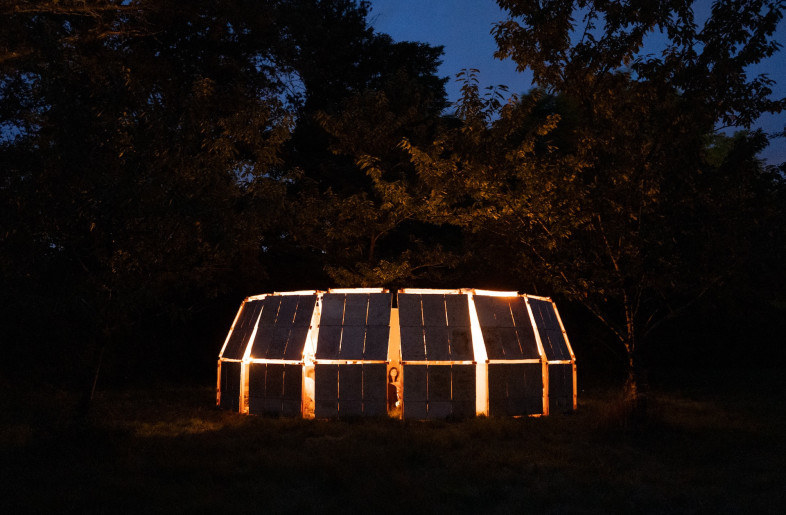
Fix, reuse, reinvent. These 4 low-impact scenographies put circular design on show
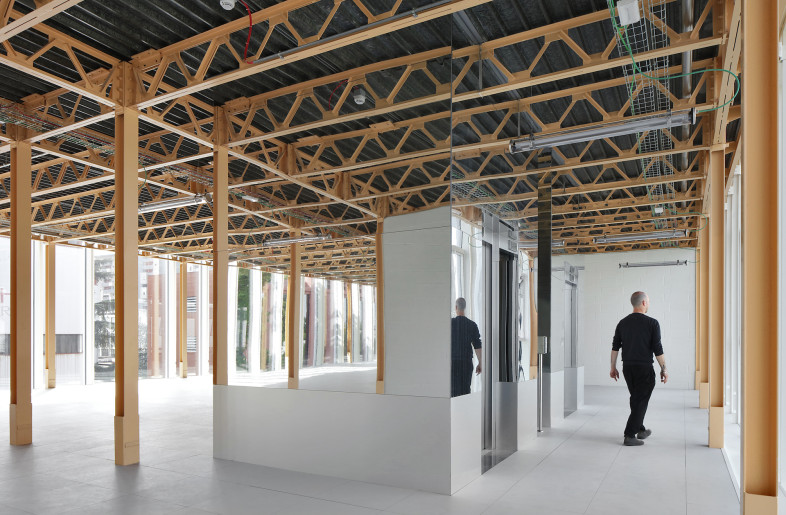