The New Design Factory: Why the future of architecture depends on emerging technology
-cover.jpg)
Architect-professors Carlo Ratti and Philip Yuan explain why fellow architects must adopt new technologies and construction methods for the sake of the profession’s future.
Create a free account to read the full article
Get 2 premium articles for free each month
Related Articles
MORE Technology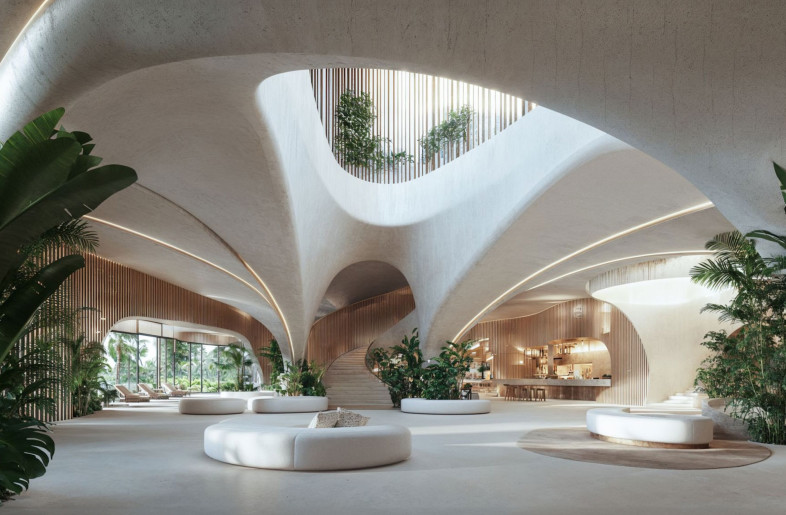
Will AI boost the lifespan of our buildings? A resounding yes, from this tech-first studio
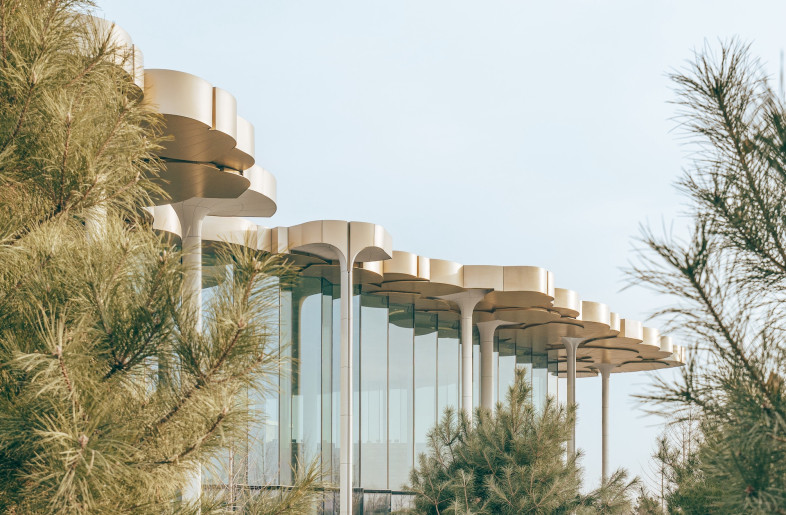
How the modern library is capturing a digital generation's attention
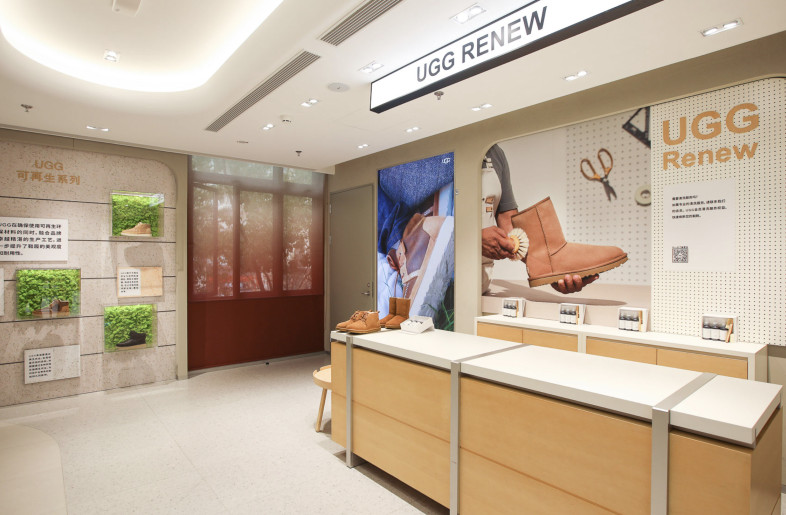
Report Recap: How modern living, work and play practices will manifest in our built environment
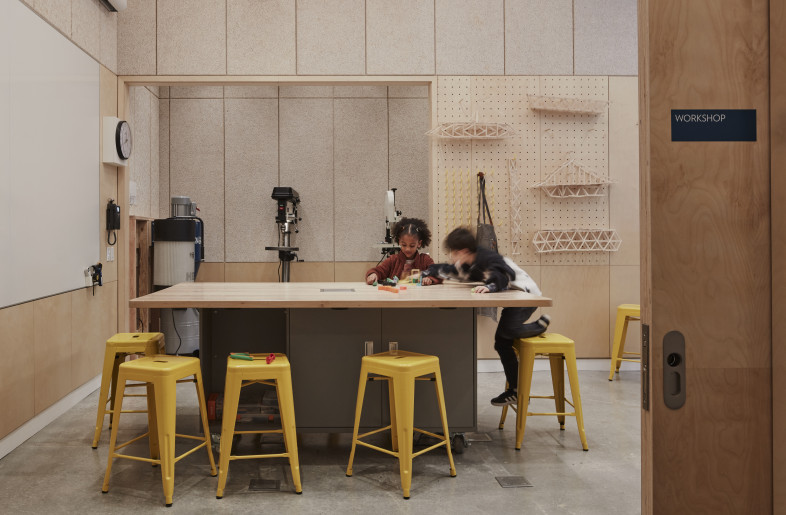
What kind of spaces do educators need for teaching tech? Here's an example
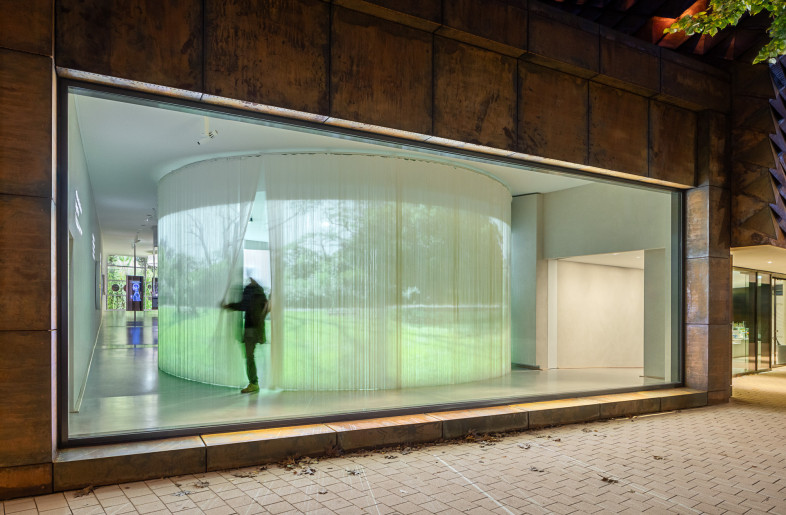
Exhibitions are for feeling, smelling and tasting, not just viewing, this aroma experience shows
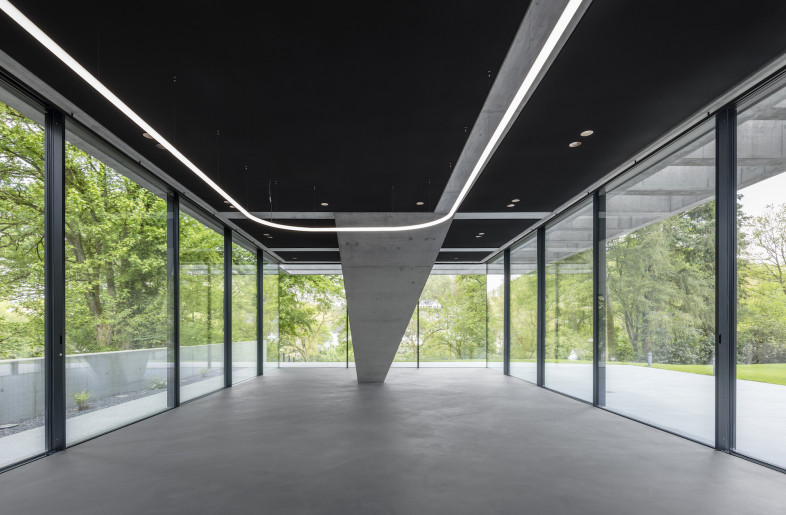
In this tech company's new space, fixtures are stripped back to the essentials. Here’s why
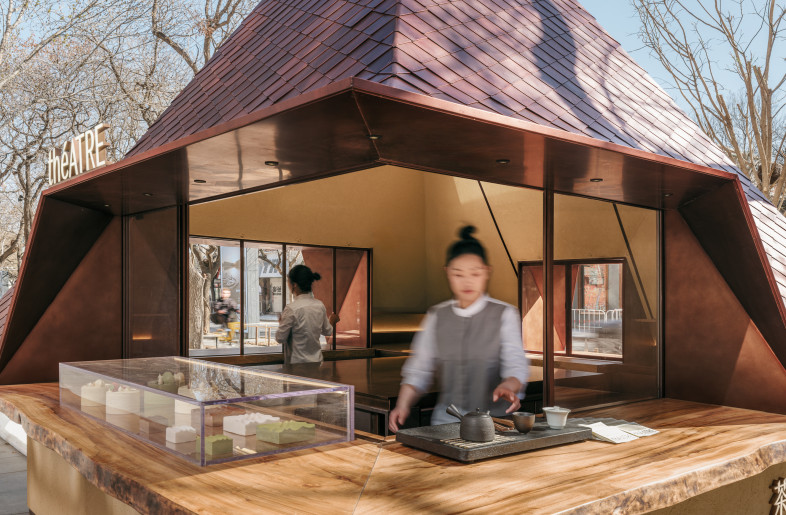
What are the factors propelling hospitality forward amid rapid expansion?
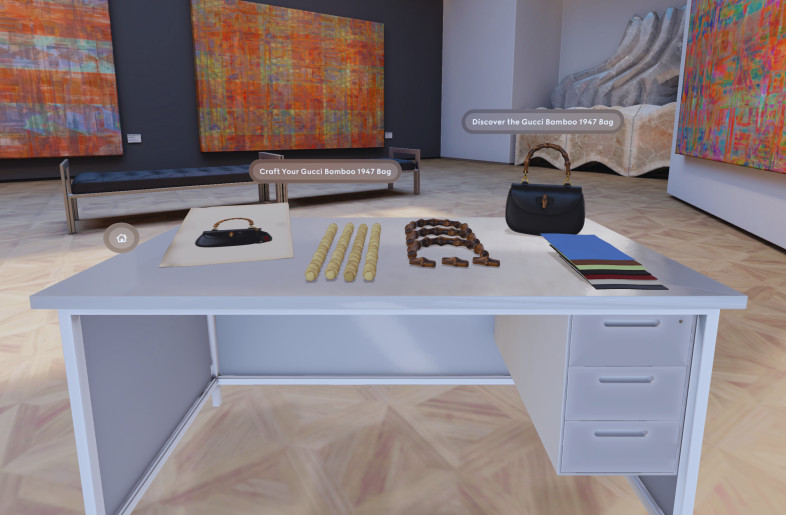
How do we shape tomorrow’s retail landscape?
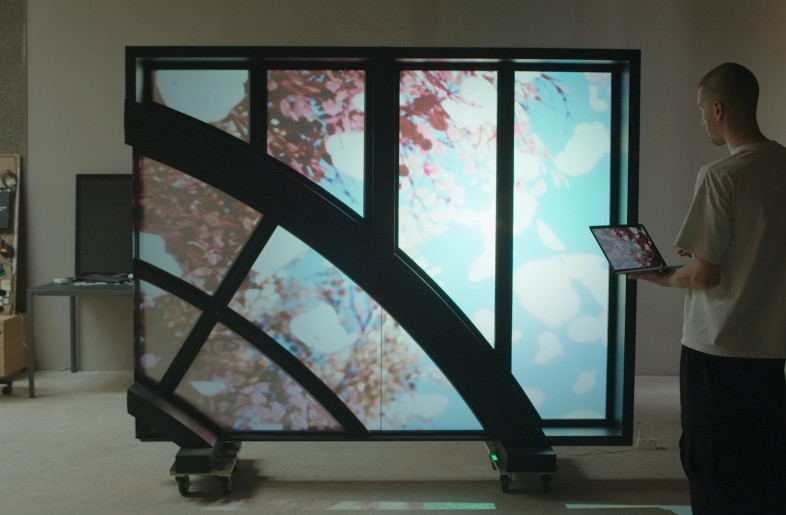
From AI to phygital design, discover 2024’s 5 top articles on everything technology
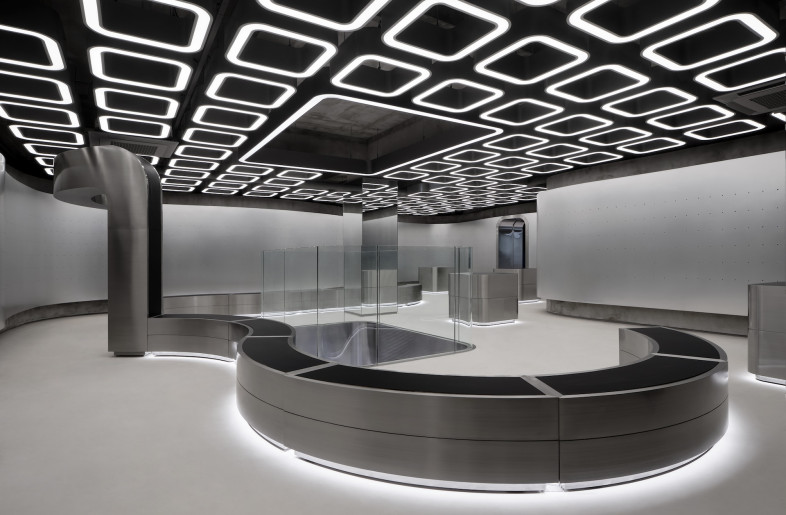