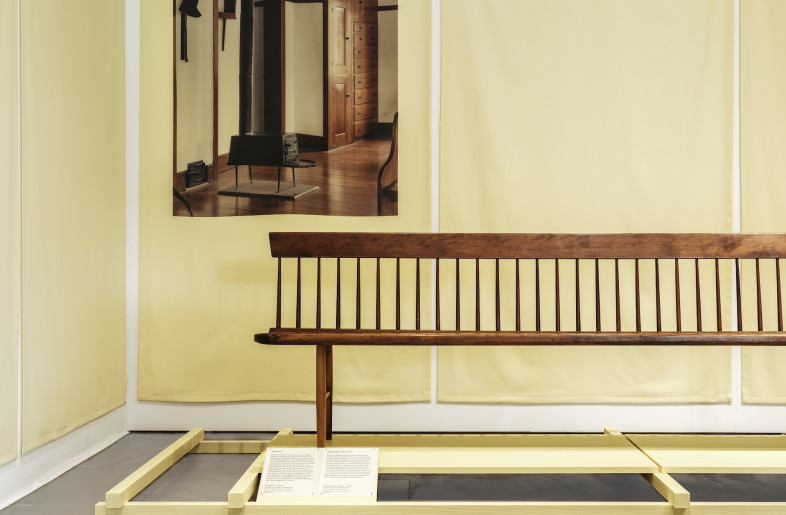
Formafantasma brings Shaker values to its exhibition design for Vitra Design Museum
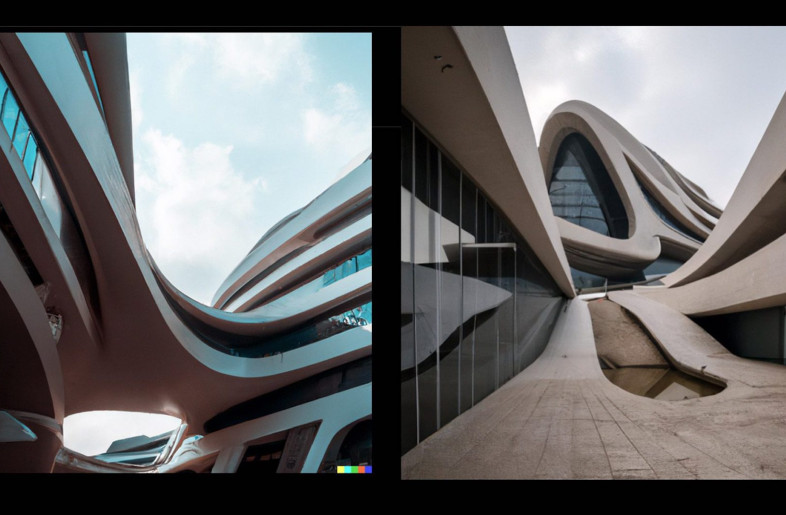
Will interior designers be replaced by AI? 4 insights search for answers.

What does contemporary design look like in a post-socialist, heritage city?
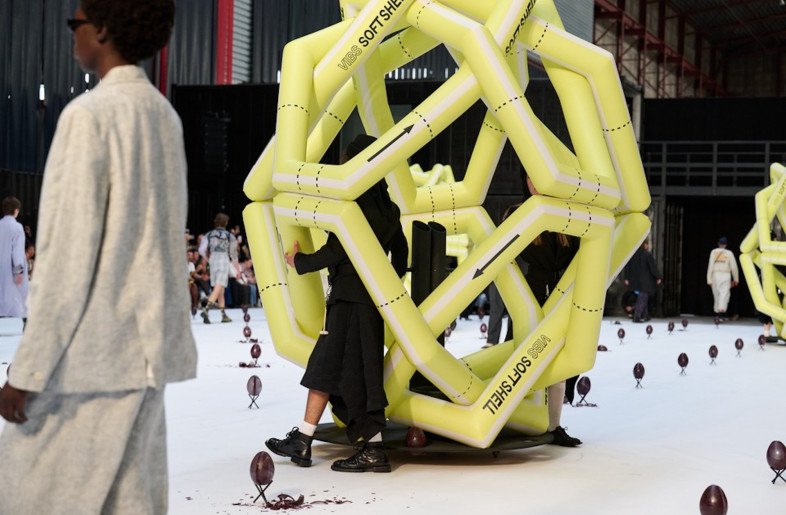
Henrik Vibskov’s SS26 fashion show builds a world with genuine care
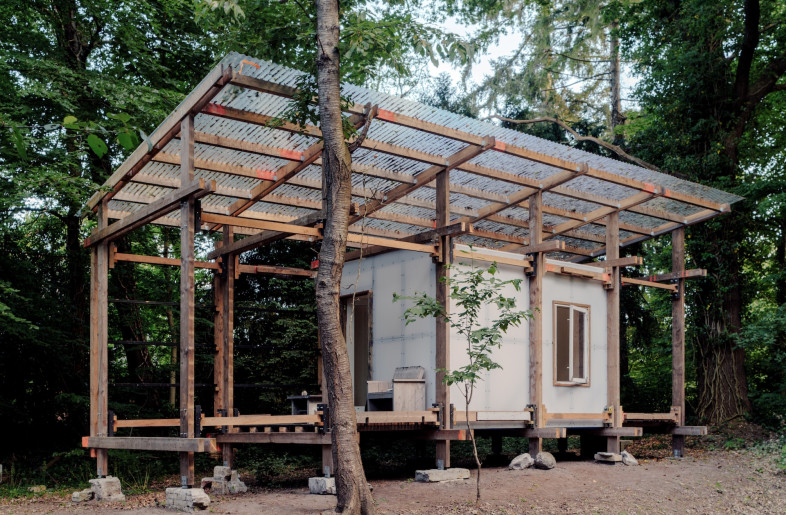
What if the contingency plan is the original plan? A hyper-local, non-extractive pavilion finds out
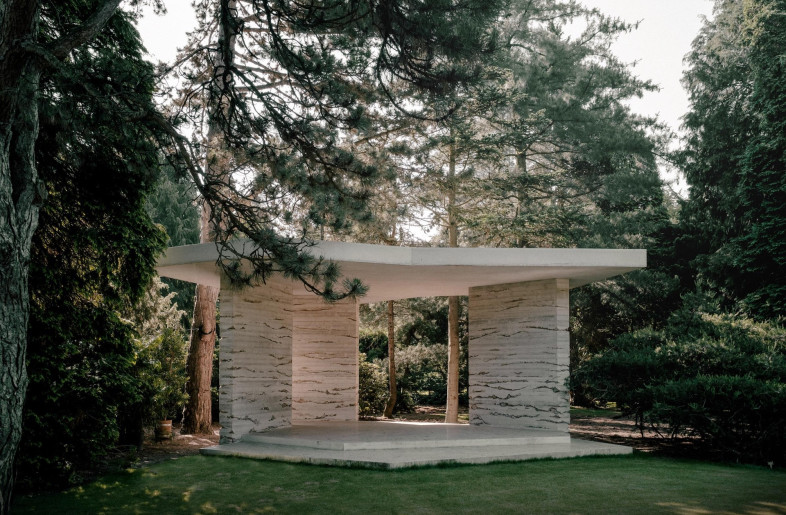
Are we ignoring the acoustic potential of public space?
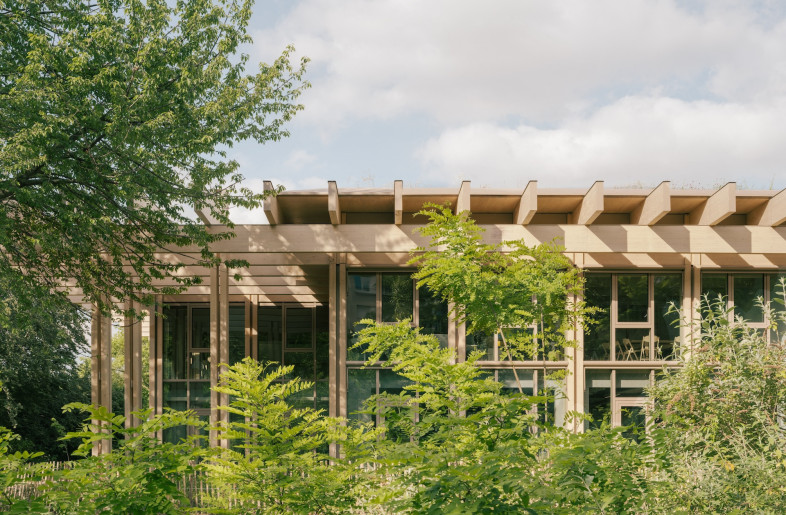